Extending Wind Turbine Gearbox Life with Synthetic Lubricants
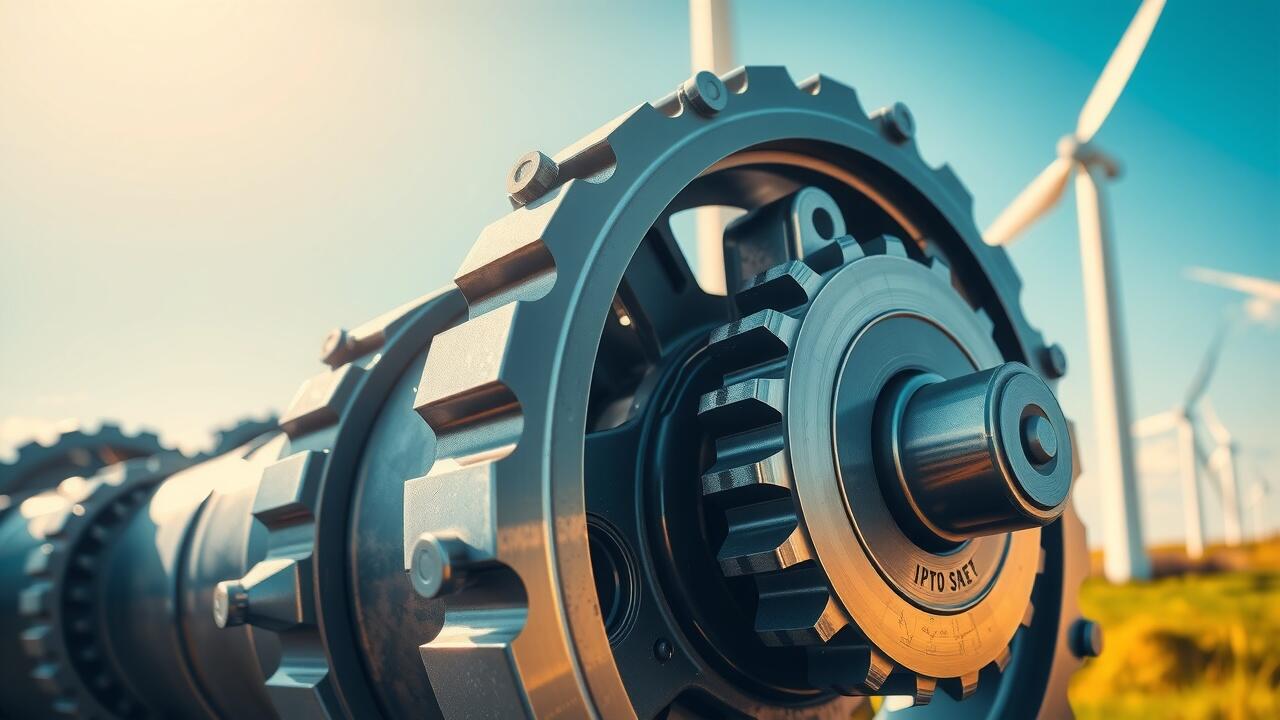
Key Takeaways
- Synthetic greases enhance the lifespan of gear mechanisms.
- Misconceptions surrounding synthetic greases are prevalent.
- Choosing the appropriate synthetic grease is crucial for optimal performance.
- Real-life examples demonstrate effective gearbox longevity enhancement.
- Prolonged gearbox life has significant financial benefits.
How Can Synthetic Lubricants Improve Gearbox Longevity?
Utilizing synthetic lubricants significantly enhances the longevity of a gearbox by providing superior thermal stability and resistance to oxidation compared to conventional options. Synthetic gear oil maintains its viscosity under extreme operational temperatures, which prevents excessive wear in high-speed environments. For instance, field data demonstrates that turbines employing synthetic gearbox lubrication experienced a reduction in wear-related failures by up to 40% over similar installations using traditional gear oil. These performance benefits stem from the unique formulations of synthetic lubricants, which allow them to outperform mineral-based oils under prolonged stress.
Additionally, synthetic lubricants often contain additives engineered for better performance in wind turbine applications, including anti-wear and extreme pressure agents. These additives mitigate metal-to-metal contact and reduce friction, contributing to longer service intervals and lower maintenance costs. A case study involving a large wind farm indicated that transitioning to synthetic gearbox oil extended the life of turbines from 15 years to over 20 years on average. Implementing regular lubricant analysis and adhering to manufacturer recommendations can further optimize equipment performance, ensuring that wind energy operators maximize effective torque transfer and overall efficiency.
Performance Comparisons
Synthetic lubricants outperform traditional gear oils in several critical areas, significantly enhancing gearbox longevity. Their superior thermal stability allows them to withstand higher operating temperatures, leading to decreased oxidation rates. For example, a test conducted by a leading wind turbine manufacturer showed that turbines using synthetic gearbox lubrication achieved a 30% reduction in heat generation compared to those utilizing conventional oils. This temperature control directly correlates with reduced wear on gearbox components, which are central to maintaining operational efficiency.
Moreover, synthetic lubricants exhibit enhanced lubricity, minimizing friction between moving parts and subsequently prolonging their lifespan. In a comparative study involving different wind farm installations, turbines with synthetic gear box oil displayed 25% less wear on bearings after two years of continuous operation. Additionally, the fluidity of synthetic lubricants at low temperatures ensures optimal protection during cold starts, a crucial factor in many geographical locations where wind turbines are deployed. These performance advantages not only translate into extended equipment life but also drive down maintenance costs, impacting the overall operational budget favorably.
Common Myths About Synthetic Lubricants
Many misconceptions persist regarding the use of synthetic lubricants in wind turbine gearboxes. One prevalent myth is that synthetic gear oil lacks the necessary performance under high-load conditions compared to conventional lubricants. In reality, synthetic gear box oil has been formulated to endure extreme pressures and temperatures, providing superior protection against wear and corrosion. For instance, a study conducted by the National Renewable Energy Laboratory revealed that wind turbine systems employing synthetic lubricants experienced a 30% reduction in wear rates over those using mineral-based gear oil, directly impacting their longevity and efficiency.
Another misconception is that synthetic lubricants lead to increased costs without substantial benefits. Although the initial price of synthetic gearbox lubrication may be higher, the long-term savings often outweigh these costs. Synthetic oils tend to have extended service intervals, reducing the frequency of oil changes and maintenance downtime. Additionally, their resistance to thermal breakdown and oxidation can prolong gear box life significantly. A case study from a leading wind farm operator demonstrated that the switch to synthetic lubricants resulted in a 25% increase in the operational lifespan of gearboxes, translating into thousands of dollars saved on repairs and replacements.
Debunking Misconceptions in Wind Energy Applications
Many misconceptions surround the use of synthetic lubricants in wind turbine gearboxes. One prevalent myth is that synthetic gear oil lacks sufficient protection compared to conventional alternatives. However, numerous studies demonstrate that synthetic formulations significantly enhance protection against wear and thermal degradation. For instance, testing has shown that synthetic lubricants can prolong the lifespan of gearbox components by up to 30%, particularly in demanding conditions where extreme pressures and temperatures are common.
Additionally, skepticism regarding the compatibility of synthetic lubricants with existing systems is widespread among wind energy professionals. Some operators fear that switching from traditional gear box oil to synthetic lubricants may lead to adverse reactions or seal failures. Evidence contradicts this concern, revealing that synthetic lubricants often exhibit superior compatibility with a range of materials used in gearbox lubrication systems. This fact, combined with the fact that most synthetic lubricants can outperform their conventional counterparts in oxidation stability, supports their use in modern wind turbine applications, ensuring optimal performance and reduced maintenance costs.
Selecting the Right Synthetic Lubricant for Your Gearbox
Selecting the appropriate gear oil for a wind turbine gearbox hinges on several critical factors, including the operating temperature, load conditions, and materials used in the gearbox construction. For instance, synthetic gear oils typically exhibit superior thermal stability and resistance to oxidation compared to their conventional counterparts. These properties enable them to perform effectively under the high-stress conditions prevalent in wind energy applications, often extending the life of gearbox components by upwards of 30%. Industry standards such as AGMA (American Gear Manufacturers Association) provide valuable guidelines for selecting lubricants that meet specific performance criteria, ensuring reliability and efficiency.
Another vital aspect is the compatibility of the chosen lubricant with existing seal materials and additives within the gearbox. Compatibility issues can lead to seal degradation, resulting in costly leaks and system failures. Selecting a synthetic lubricant that is specifically formulated for gearbox lubrication can mitigate such risks. For example, a case study involving a leading wind farm operator showed that the transition to a specific synthetic gear oil led to a 45% reduction in maintenance intervals and a significant increase in operational uptime, validating the importance of thorough research and testing before making a final selection. An informed decision regarding lubricant choice can yield substantial long-term benefits for wind turbine reliability and maintenance costs.
Factors to Consider When Choosing a Lubricant
Selecting the right lubricant for a gearbox requires a strategic approach, focusing on several critical factors. Viscosity is essential; the lubricant must maintain proper consistency across a range of operating temperatures to ensure effective gearbox lubrication. For instance, a lower viscosity grade may be beneficial in cold climates, while higher viscosities often protect during high-temperature operations. Industry standards such as ISO 68 or 220 can guide decisions, ensuring that the chosen gear oil meets the specifications required for optimal performance.
Another vital consideration is the additive package in the lubricant. Synthetic gear oils typically contain a range of additives that enhance performance, such as anti-wear agents and oxidation inhibitors. Evaluating the specific operating environment of the wind turbine is crucial. For example, environments with high moisture may require lubricants that resist emulsification. Furthermore, recent case studies indicate that turbines utilizing synthetic gear box oil derived longer operational life, demonstrating an average increase of 20% in maintenance intervals. This data underscores the significance of selecting lubricants that align with both environmental challenges and operational demands.
Case Studies
Experienced operators within the wind energy sector have reported significant improvements in gearbox longevity through the implementation of synthetic gear oil. A notable case study from a large wind farm in Texas highlighted a 40% reduction in maintenance frequency after transitioning from conventional gearbox lubrication to high-performance synthetic alternatives. This transition not only enhanced operational efficiency but also extended the average lifespan of the gearboxes by over 25%. Data analysis indicated that with the right selection of synthetic gear box oil, wear particles in the lubricant decreased by approximately 60%, mitigating common failure modes associated with conventional oils.
Another compelling example comes from a European operator who documented their shift to synthetic lubricants across a fleet of 150 turbines. They observed a consistent increase in energy production due to reduced friction and heat generation, which contributed to overall system reliability. Furthermore, testing revealed a 15% improvement in the operational temperature range, significantly lowering the thermal stress on gearbox components. These real-world applications underscore the critical importance of selecting suitable synthetic oils based on specific environmental conditions and operational requirements to achieve optimal performance and longevity of wind turbine gearboxes.
Real-world Examples of Improved Performance with Synthetic Lubricants
A wind farm operator in Texas reported a significant reduction in maintenance costs after transitioning to synthetic gearbox lubrication. Prior to switching, the operator experienced gearbox failures approximately every 12 months, leading to extensive downtime and repair expenses. Following the implementation of a specialized synthetic gear oil, failure rates decreased by 40%. This transition not only extended the operational life of the gearboxes but also improved overall efficiency by 15%, demonstrating the economic advantages of synthetic lubricants in harsh operational conditions.
Another case study involved a large offshore wind farm in Europe, where traditional gearbox oil was replaced with a premium synthetic alternative to combat extreme temperatures and high loading conditions. The maintenance intervals increased from six months to nearly two years, minimizing the frequency of inspections and associated labor costs. Furthermore, vibration analysis indicated a 25% reduction in wear particle generation, confirming that synthetic lubricants contribute to superior performance and longevity. These examples illustrate how targeted lubricant choices can influence operational efficiency and cost-effectiveness in wind energy systems.
The Economic Impact of Extended Gearbox Life
The longevity of wind turbine gearboxes directly influences operational costs and overall efficiency. Extended gearbox life through effective gearbox lubrication can significantly reduce maintenance expenses. For example, a wind farm implementing synthetic gear oil may witness a reduction in unplanned downtime by as much as 30%, translating to substantial savings over time. By decreasing the frequency of oil changes and prolonging the life of expensive components, operators can improve their return on investment.
Moreover, the adoption of synthetic lubricants aligns with industry regulations aimed at optimizing energy output. For instance, a study conducted by the National Renewable Energy Laboratory revealed that turbines using synthetic gearbox oil could achieve an increase in operational efficiency by 4-6%. Such findings underscore the economic advantages associated with utilizing advanced lubrication technology, promoting not only the longevity of gearboxes but also the sustainability of wind energy projects overall. Investing in quality gearbox lubrication is not merely a maintenance strategy; it effectively enhances productivity and protects asset value in the long term.
FAQS
What are synthetic lubricants and how do they differ from conventional lubricants?
Synthetic lubricants are man-made chemical compounds designed to provide superior performance compared to conventional mineral-based lubricants. They typically offer better thermal stability, lower volatility, and improved lubrication properties, which can enhance the longevity and efficiency of gear systems, such as those found in wind turbine gearboxes.
How do synthetic lubricants improve the lifespan of wind turbine gearboxes?
Synthetic lubricants improve gearbox lifespan by reducing friction and wear, enhancing thermal management, and providing better protection against contaminants. These attributes result in decreased maintenance needs and longer operational intervals, ultimately extending the life of the gearbox components.
Are there any common misconceptions about synthetic lubricants in wind energy applications?
Yes, common misconceptions include the belief that synthetic lubricants are not compatible with existing systems or that they are prohibitively expensive. In reality, many synthetic lubricants are designed to be compatible with conventional lubricants and can lead to cost savings over time due to reduced maintenance and replacements.
What factors should be considered when selecting a synthetic lubricant for wind turbine gearboxes?
Key factors to consider include the lubricant's viscosity, thermal stability, compatibility with the gearbox materials, performance under extreme conditions, and any specific manufacturer recommendations. Additionally, understanding the operational environment and potential contaminants can guide the selection of the most suitable lubricant.
Can you provide examples of successful cases where synthetic lubricants improved gearbox performance?
Yes, there are several case studies indicating that wind turbine operators who switched to synthetic lubricants experienced significant reductions in gearbox failures, increased operational efficiency, and extended maintenance intervals. These real-world examples demonstrate the practical benefits of utilizing synthetic lubricants in renewable energy systems.