Expert Analysis: Why Thermal Stability Matters in Enclosed Gear Drives
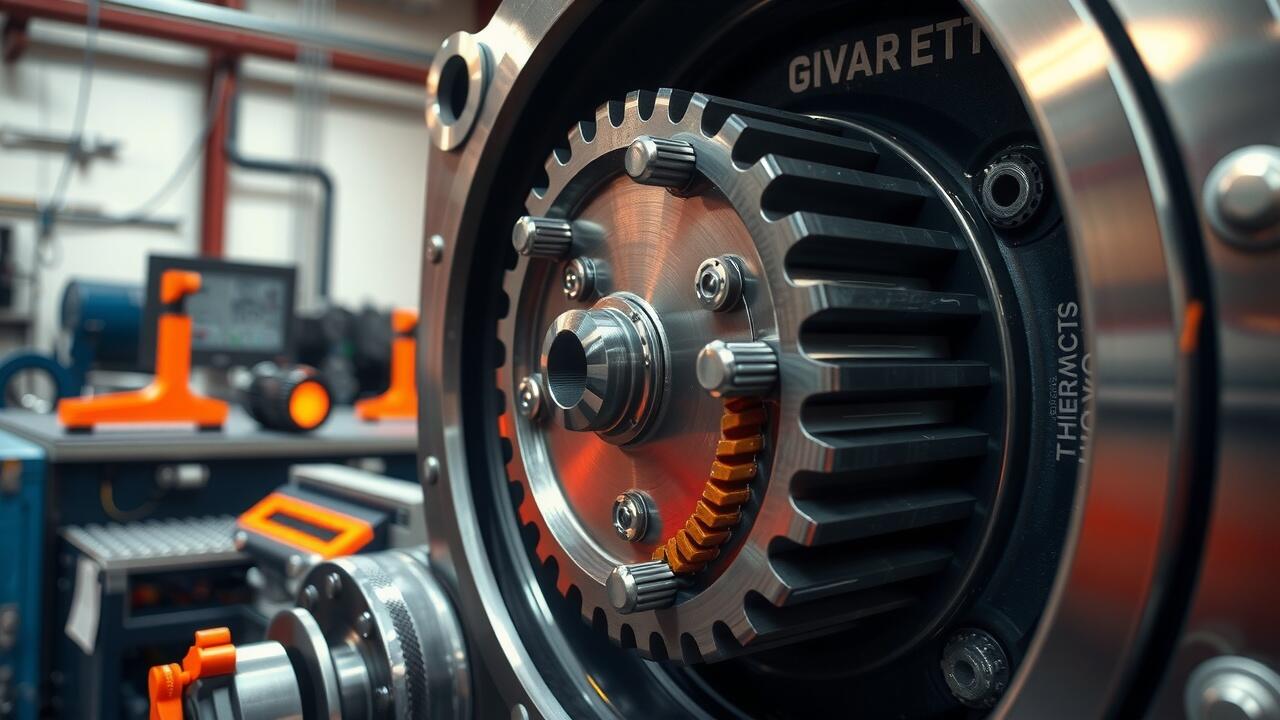
Key Takeaways
- Influence of Oils on Heat Regulation
- Evaluating Material Characteristics for Enhanced Heat Endurance
- Assessing and Observing Thermal Integrity
- Practical Uses of Temperature Consistency
- Ensuring Longevity of Gear Mechanisms Against Heat Challenges
The Impact of Lubrication on Thermal Management
Lubrication plays a critical role in the thermal management of enclosed gear drives, significantly impacting their efficiency and reliability. Proper gear oil formulations are designed to reduce friction and dissipate heat within the gearbox. For instance, synthetic gear box oil often exhibits superior thermal stability compared to traditional mineral oils, maintaining a consistent viscosity across temperature variations. This characteristic is crucial in high-load applications, where temperature increases can lead to accelerated wear and potential failure. Testing has shown that systems utilizing advanced lubrication can experience a reduction in operating temperatures by up to 15% compared to those with subpar lubricants.
Furthermore, ensuring adequate gearbox lubrication extends not only the life of the gear set but also improves overall system performance. Implementing periodic monitoring of oil viscosity and thermal properties enables early detection of lubrication breakdown, which can prevent catastrophic equipment failure. For example, a study of industrial gear drives showed that consistent oil analysis led to a 20% decrease in maintenance costs and a substantial reduction in unplanned downtime. Understanding the specific lubricant requirements for each application is vital. Selecting the right gear oil based on operational conditions will optimize heat transfer, enhance equipment life, and ultimately drive operational efficiency.
How Can Proper Lubrication Improve Thermal Stability?
Effective lubrication plays a critical role in enhancing thermal stability within enclosed gear drives. A thorough understanding of the specific properties of gear oil can significantly impact temperature control. For instance, specialized gear box oil designed with a high viscosity index can reduce friction and heat generation during operation. This formulation ensures a consistent lubricating film even under varying temperatures, thereby maintaining stability and efficiency. Furthermore, employing synthetic gear oils can lead to improved thermal performance, as they typically exhibit superior thermal resistance compared to conventional oils. Studies indicate that synthetic lubricants can increase the lubrication lifespan by up to 50%, thus further mitigating the risk of overheating.
To maximize thermal management, industries should adopt a proactive approach in gearbox lubrication strategies. Regular monitoring of lubricant conditions is vital for maintaining thermal performance. Implementing oil analysis programs can provide insights into viscosity breakdown, particle contamination, and thermal degradation. For instance, industry standards recommend oil analysis every 3,000 operating hours or in accordance with manufacturers’ recommendations. By adhering to these best practices, organizations can not only prolong equipment life but also avert costly downtime associated with overheating failures.
Analyzing Material Properties for Better Heat Resistance
The selection of materials for enclosed gear drives is critical for enhancing thermal resistance and operational integrity. Advanced alloys, such as high-strength steel and aluminum composites, have demonstrated superior heat resistance and durability under intense load conditions. For instance, AISI 4340 alloy steel, often used in heavy-duty applications, allows gear systems to withstand operational temperatures up to 200°C without compromising structural integrity. This capability reduces downtime and maintenance costs, emphasizing the necessity of rigorous material testing in alignment with ASTM standards.
Moreover, the compatibility of lubrication with selected materials influences thermal stability outcomes significantly. Using high-performance gear oils formulated to withstand elevated temperatures ensures optimal gearbox lubrication. For example, synthetic oils often provide improved thermal stability compared to mineral oils, maintaining their viscosity across a broader temperature range. Organizations leveraging these advanced lubricants have reported a decrease in friction-related wear by over 30%, extending the lifespan of critical components. Understanding materials and their interactions with lubricants fosters a proactive approach to managing heat in gear drives, paving the way for enhanced operational efficiency.
What Materials are Best Suited for High-Temperature Environments?
Materials that exhibit excellent thermal stability are essential for managing heat in enclosed gear drives. Metals such as high-alloy stainless steel and tool steel provide superior resistance to thermal expansion and deformation. These materials withstand operating temperatures that can exceed 200 degrees Celsius, ensuring the structural integrity of the gearbox under high-load conditions. Additionally, advanced ceramics and composite materials offer significant thermal resistance while maintaining lightweight characteristics, making them suitable for various high-temperature environments.
When selecting suitable materials, the compatibility with lubrication systems becomes critical. For example, gear box oil plays a vital role in cooling and reducing friction between moving components. Selecting synthetic gear oil can further enhance thermal stability, allowing consistent performance even when temperatures spike. According to industry standards, the use of lubricants with high thermal stability helps prevent oxidative breakdown, ensuring longer service life for both the lubricant and gearbox components. Companies that prioritize material selection and lubrication strategies consistently report improved operational efficiency and reduced maintenance costs, affirming the importance of careful material analysis in gear drive design.
Testing and Monitoring Thermal Stability
Thermal stability in enclosed gear drives hinges on reliable testing and monitoring practices. Infrared thermography serves as a valuable tool for assessing surface temperatures during operation, enabling technicians to identify hotspots that may indicate potential failure modes. For example, a study indicated that gearboxes equipped with synthetic gear oil showed a 15% reduction in temperature fluctuations compared to those using traditional mineral oils. This highlights the crucial role of advanced gearbox lubrication in maintaining optimal performance and extending equipment life.
Data acquisition systems can track thermal performance over long periods, allowing for the analysis of trends that inform maintenance schedules. Regular monitoring can help detect anomalies, preventing costly failures. Implementing vibration analysis alongside thermal imaging provides a comprehensive overview of gearbox health. This multifaceted approach supports industry standards such as ISO 9001, ensuring that gear drives operate efficiently under varying thermal loads. Taking proactive steps in monitoring not only enhances durability but also supports overall operational efficiency.
What Methods Are Available for Assessing Thermal Performance?
Thermal performance in enclosed gear drives can be accurately assessed through a combination of empirical testing and advanced simulation techniques. Thermal imaging cameras are commonly employed to visualize heat distribution, identifying hotspots that may indicate potential failure points. Additionally, utilizing thermocouples and infrared sensors allows for continuous temperature monitoring during operation, providing real-time data that can be compared against baseline performance metrics. This approach helps in evaluating the effectiveness of gear oil or gearbox lubrication strategies, ensuring proper thermal management throughout the drive.
Finite element analysis (FEA) plays a crucial role in predicting thermal behavior under various loading conditions and environmental factors. By simulating different operational scenarios, engineers can assess how material properties influence heat dissipation. Case studies have demonstrated that optimal gearbox lubrication significantly enhances thermal stability, with analyses revealing reductions in peak operating temperatures by up to 20%. Incorporating these methodologies into the design process leads to proactive measures that mitigate thermal issues, ultimately extending the lifespan and reliability of gear drives.
Real-World Applications of Thermal Stability
Effective thermal management within gear drives is crucial for industries such as automotive and aerospace. For instance, in high-performance racing environments, the reliability of gear oil significantly influences the overall system’s efficiency and durability. When subjected to extreme conditions, inadequate gearbox lubrication can lead to lubricant degradation, causing increased friction and ultimately gear failure. Industry standards emphasize regular monitoring of lubricant temperatures and properties to ensure optimal performance, with many organizations implementing advanced thermal analysis tools to detect potential failures before they occur.
Case studies reveal that companies using high-performance gear box oil have experienced up to a 30% reduction in operating temperatures. This improvement leads to extended service life and reduced maintenance costs. The aerospace sector, heavily regulated by FAA standards, showcases advanced thermal stability measures, often opting for synthetic gear oils designed for high-temperature applications. Continuous improvements in thermal stability foster innovations that not only enhance performance but also align with sustainability goals through reduced energy consumption and waste.
How Do Industries Benefit from Enhanced Thermal Management in Gear Drives?
Enhanced thermal management in gear drives notably reduces the risk of premature equipment failure, a concern prevalent in various industries such as automotive and manufacturing. By utilizing high-quality gear oil specifically formulated for elevated temperatures, organizations can improve the operational lifespan of gear assemblies. Research indicates that effective gearbox lubrication can lower operational temperatures by up to 30%, which significantly reduces thermal stress on components. This reduction in temperature can mitigate wear and tear on bearings and gears, ultimately enhancing productivity and reducing maintenance costs.
Industries utilizing advanced thermal stability measures often achieve operational efficiencies that translate into tangible financial benefits. For example, a large-scale manufacturing facility that implemented optimized gearbox lubrication saw a 15% increase in machinery uptime. The choice of synthetic gear box oil, engineered to perform under high thermal loads, can maintain optimal viscosity levels even in extreme conditions. Their results illustrate how comprehensive thermal management strategies foster reliability, ensuring that gear drives perform consistently within designated parameters while meeting stringent industry standards.
Future-Proofing Gear Drives Against Thermal Issues
Incorporating advanced thermal management techniques can significantly enhance the longevity and efficiency of gear drives. Regular monitoring and the use of high-performance gear oil can prevent overheating by ensuring optimal lubrication even under extreme operational conditions. For example, synthetic gear oils demonstrate superior thermal stability and can extend the lifespan of components by as much as 30%, particularly in applications subjected to consistent high temperatures. Industries utilizing heavy machinery must prioritize gearbox lubrication that meets or exceeds the specifications outlined in API standards to maximize equipment reliability while minimizing breakdown risks.
When selecting materials for gear drive manufacturing, engineers can make a substantial impact on thermal resistance. High-performance alloys and composites resist warping and degradation more effectively than traditional materials. A case study involving the aerospace sector revealed that the implementation of specialized heat-treated steels resulted in a 25% reduction in thermal expansion, significantly enhancing gear performance under stress. To future-proof gear drives, organizations should invest in ongoing thermal performance assessments, including thermal imaging and temperature mapping, ensuring that potential issues are identified and addressed proactively.
FAQS
What is thermal stability in enclosed gear drives?
Thermal stability in enclosed gear drives refers to the ability of the gear system to maintain performance and structural integrity under varying temperature conditions, ensuring efficient operation and longevity.
Why is lubrication important for thermal management in gear drives?
Lubrication plays a critical role in thermal management by reducing friction and heat generation between moving parts, thereby enhancing thermal stability and preventing overheating.
What materials are recommended for high-temperature environments in gear drives?
Materials such as high-performance alloys, ceramics, and specially formulated polymers are recommended for high-temperature environments as they exhibit superior heat resistance and stability.
What methods can be used to assess the thermal performance of gear drives?
Common methods for assessing thermal performance include thermal imaging, temperature monitoring sensors, and experimental testing under controlled conditions to evaluate heat generation and dissipation.
How do industries benefit from improved thermal management in gear drives?
Industries benefit from improved thermal management through increased operational efficiency, reduced maintenance costs, enhanced reliability, and prolonged equipment lifespan, ultimately leading to better productivity and reduced downtime.